Plastic extrusion for streamlined, flexible manufacturing solutions
Plastic extrusion for streamlined, flexible manufacturing solutions
Blog Article
Key Advantages and Considerations of Carrying Out Plastic Extrusion in Your Projects

Understanding the Basics of Plastic Extrusion
Plastic extrusion, a staple in the manufacturing sector, is a procedure that includes melting raw plastic material and improving it right into a continuous profile. This account, when cooled, can be cut right into preferred lengths or curled for later use. The charm of plastic extrusion hinges on its convenience. A vast array of products, from piping to home window frameworks, can be produced. The procedure calls for an extruder, an elaborate machine with a warmed barrel, a rotating screw, and a die at the end. The plastic product, in the type of pellets, is fed right into the extruder, where it's thawed and forced via the die, taking its shape. The selection of plastic and the style of the die determine the item's qualities.

The Economic Benefit of Plastic Extrusion
The economic advantage of plastic extrusion exists predominantly in 2 locations: cost-effective material manufacturing and beneficial manufacturing speeds. With plastic extrusion, services can generate high quantities of material at a lower expense contrasted to various other methods. The procedure boasts an outstanding production speed, substantially reducing time and further enhancing its economic feasibility.
Economical Product Manufacturing
A substantial advantage of plastic extrusion is its impressive cost-effectiveness. This production process permits constant, high-volume manufacturing with minimal waste, which equates right into reduced costs. The raw products used, usually plastic pellets, are relatively affordable compared to various other materials (plastic extrusion). The procedure itself requires less power than many various other manufacturing methods, additionally reducing costs. Furthermore, the extrusion process enables for a high level of precision fit the plastic, minimizing the requirement for expensive post-production alterations or corrections. Additionally, the longevity and long life of extruded plastic products often mean much less need for substitutes, adding to long-lasting savings. All these aspects make plastic extrusion a highly affordable option for many tasks, providing an attractive equilibrium between cost and efficiency.
Beneficial Manufacturing Speeds
While maintaining the cost-effectiveness of the materials, an additional noteworthy advantage of plastic extrusion depends on its rapid production rates. This efficiency in the manufacturing procedure is credited to the continuous nature of the extrusion procedure, permitting high-volume manufacturing in a relatively short time span. The rate of manufacturing directly correlates to a reduction in labor prices and an increase in output, consequently boosting the overall economic practicality of the procedure. In addition, the fast-paced production does not jeopardize the top quality of the end product, guaranteeing dependable and constant outcomes. This mix of rate, top quality, and cost-effectiveness underscores the significant economic advantage of executing plastic extrusion in various projects.
Flexibility and Customization: The Toughness of Plastic Extrusion
Among the popular strengths of plastic extrusion exists in its flexibility and customization possibility. These high qualities open the door to endless style possibilities, offering producers the ability to customize products to details requirements. This heightened degree of customization not just enhances item functionality yet likewise significantly improves product originality.
Limitless Layout Possibilities
Plastic extrusion radiates in its capacity to provide almost endless design possibilities. This approach offers liberty to create complex shapes and detailed profiles, an accomplishment hard to attain with other construction strategies. Owing to the fluid nature of liquified plastic, the procedure is flexible enough to produce a diverse variety of sizes, dimensions, and types. The plastic can be adjusted to match unique specs, enabling the manufacturing of customized geometries and meeting certain customer needs. Plastic extrusion can handle a variety of plastic types, broadening its application extent. This versatile technique, for that reason, serves a vast array of industries from building to automobile, product packaging to electronic devices, and past. With plastic extrusion, the layout opportunities are basically endless.
Improving Product Uniqueness
The flexibility of plastic extrusion can significantly boost item uniqueness. This procedure allows developers to try out different shapes, sizes, and shades, providing the flexibility to produce distinct products that attract attention in the market. It is this modification that offers an unique identity per item, differentiating it from its competitors.
Along with its visual advantages, the customizability of plastic extrusion additionally uses useful benefits. Developers can customize the residential properties of the plastic according to the certain needs of the application, boosting the product's functionality. They can make the plastic more adaptable, much more you can find out more sturdy, or a lot more immune to warm, depending on what the product needs. Thus, plastic extrusion not only enhances product originality but additionally its utility and bankability.
Style Limitations in Plastic Extrusion: What You Required to Know
How can make limitations potentially influence the process of plastic extrusion? While plastic extrusion is versatile, design constraints can curtail its advantages. Particular complex designs might not be viable due to the restrictions of the extrusion procedure, possibly restricting the creation of complex accounts. The procedure is much less suitable for hollow or multi-chambered frameworks. In addition, the extrusion procedure check it out might not always offer the preferred surface area coating, specifically for those requiring high gloss or optical clarity. Material choice can likewise present obstacles, as not all polymers are suitable for extrusion. High-temperature resistant plastics, for instance, may present problems. Comprehending these restrictions is critical for effective implementation of plastic extrusion in your projects. plastic extrusion.
Evaluating the Ecological Influence of Plastic Extrusion
While comprehending design restrictions is a substantial element of plastic extrusion, it is just as important to consider its ecological effects. The process of plastic extrusion includes melting plastic products, potentially launching harmful gases into the setting. Using recycled plastic materials in the extrusion procedure can reduce environmental influence.
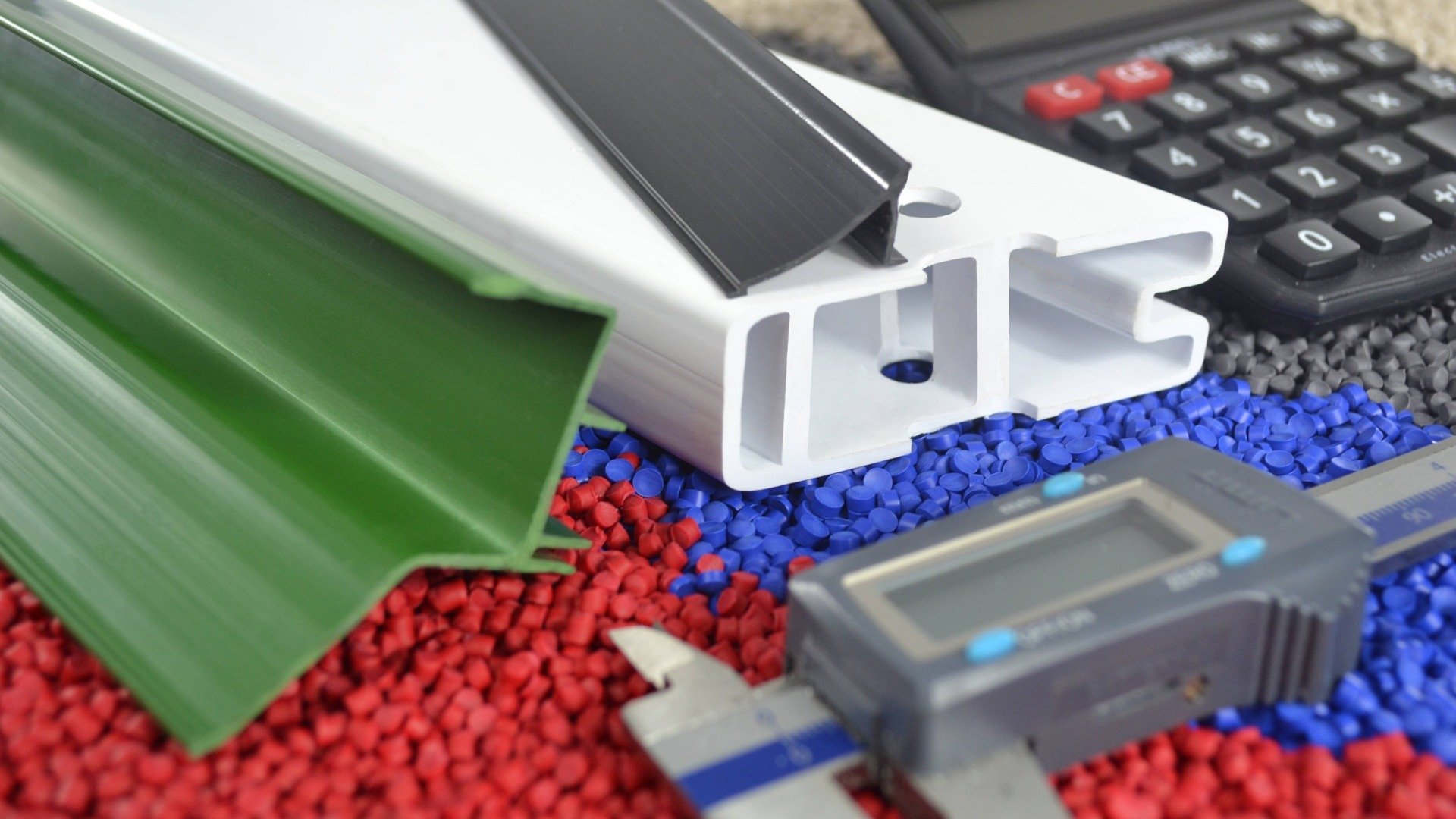
Instance Study: Successful Projects Utilizing Plastic Extrusion
Success stories in the field of plastic extrusion abound, demonstrating both the flexibility and efficiency of this production process. One significant instance is the development of PVC pipes utilized in modern pipes. This procedure includes melting plastic and developing it into a constant tube, providing considerable expense and sturdiness advantages. Another successful instance is the manufacturing of plastic movie for product packaging and agriculture. Through extrusion, manufacturers can produce very personalized, slim, and robust films. Automotive industries additionally profit, utilizing extruded plastic for parts like trim or seals, boosting lorry durability. These instances illustrate plastic extrusion's crucial duty in numerous markets, confirming to its adaptability, cost-effectiveness, and reliable result.
Conclusion
In final thought, this post plastic extrusion supplies a effective and affordable method for producing complicated forms with minimal waste. Integrating plastic extrusion right into projects can lead to effective end results, as shown by numerous situation research studies.
Plastic extrusion, a staple in the production sector, is a procedure that entails melting raw plastic material and reshaping it into a continuous profile. Plastic extrusion can deal with a range of plastic kinds, broadening its application range.Just how can make constraints possibly influence the procedure of plastic extrusion? The procedure of plastic extrusion entails melting plastic products, possibly launching hazardous gases into the environment. Using recycled plastic materials in the extrusion procedure can lower ecological influence.
Report this page